Firma Lavigne zwiększa wydajność swojej produkcji z systemem DELMIA Ortems
Firma Lavigne to francuski producent ilustrowanych kalendarzy, upominków biznesowych, markowych przedmiotów reklamowych i artykułów papierniczych. Zawsze stara się reagować na nowe trendy, dostosowując swoje produkty do potrzeb rynku. Dlaczego zdecydowała się na wdrożenie kompleksowego systemu do zaawansowanego planowania i harmonogramowania produkcji DELMIA Ortems?
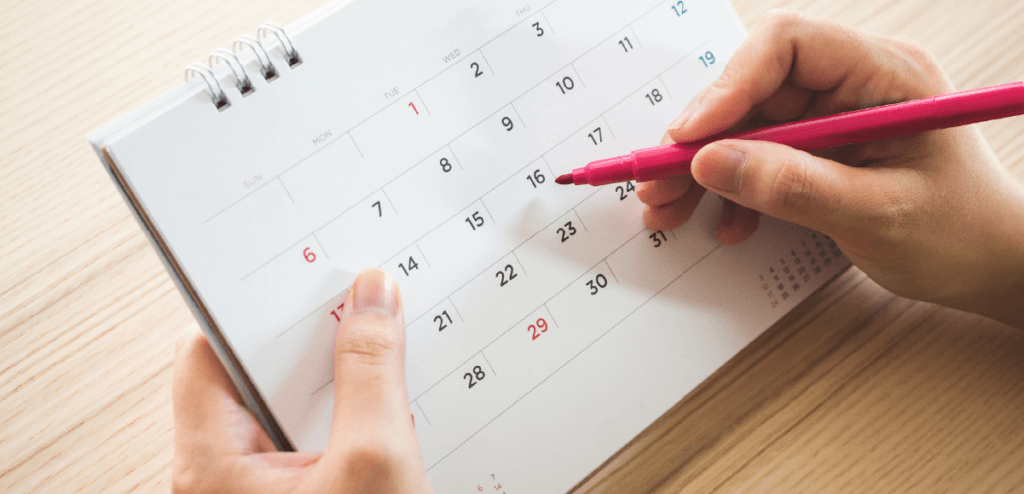
Produkcja tego przedsiębiorstwa charakteryzuje się dużą sezonowością. Aż 85% rocznego obrotu pochodzi z ostatniego kwartału roku. Przypadające na ten okres obciążenia produkcyjne stanowią duże wyzwanie dla firmy, której priorytetem jest utrzymanie wysokiego zadowolenia klienta i dotrzymanie terminów. Dodatkową trudnością są również nagłe zamówienia składane w tym okresie przez klientów.
Firma Lavigne, która wcześniej nie posiadała ustrukturyzowanego planowania, a swoje decyzje i działania w tym zakresie podejmowała w oparciu o doświadczenie i intuicję, stanęła przed koniecznością nabycia oprogramowania, które pozwoli jej uzyskać wykonalny i realistyczny plan uwzględniający dostępne zasoby i ograniczenia produkcyjne.
Lavigne zdecydowała się na rozwiązanie DELMIA Ortems przeznaczone do zarządzania wszystkimi procesami planowania firmy. System został wdrożony w 2016 roku w rekordowo szybkim czasie. Rozwiązanie tchnęło nowe życie w sposób, w jaki pracowała firma. Plan produkcji jest w pełni zoptymalizowany i elastyczny – pozwala na szybką identyfikację wąskich gardeł, wprowadzanie priorytetów zamówień czy dokonywanie szybkich zmian i modyfikacji z widocznymi konsekwencjami podjętych działań. Pracownicy posiadają całkowitą kontrolę i widoczność harmonogramu produkcji, które obecnie stanowi dla nich jedno wiarygodne źródło informacji.
Firma Lavigne dzięki wdrożeniu systemu DELMIA Ortems odniosła szereg korzyści, wśród których jako najważniejsze wskazuje:
- Zwiększenie wydajności produkcji o 30%
- Wzrost jakości obsługi zleceń produkcyjnych do poziomu 95%
- Poprawa jakości i terminowości dotrzymywania zobowiązań handlowych
- Lepsza synchronizacja przepływów zleceń produkcyjnych
- Redukcja czasów przezbrojeń maszyn
- Zmniejszenie ilości błędnych decyzji